- 会員限定
- 2019/12/11 掲載
詳説、これからの製造業に「プラットフォーム」が不可欠な理由
福本 勲
東芝 デジタルイノベーションテクノロジーセンター 参事、東芝デジタルソリューションズ ICTソリューション事業部 担当部長、中小企業診断士、PMP(Project Management Professional) 。1990年3月早稲田大学大学院修士課程(機械工学)修了。 1990年に東芝に入社後、製造業向けSCM、ERP、CRMなどのソリューション事業立ち上げやマーケティングに携わり、現在はインダストリアル IoT、デジタル事業の企画・マーケティング・エバンジェリスト活動などを担うとともにオウンドメディア「DiGiTAL CONVENTION」の編集長をつとめる。 2015年より一般社団法人 インダストリアル・バリューチェーン・イニシ アティブ(IVI)正会員となり、教育普及委員会副委員長、エバンジェリストなどをつとめる。その他、複数の団体で委員などをつとめている。主な著書に『デジタル・プラットフォーム解体新書』(共著:近代科学社) がある。主な Webコラム連載に、ビジネス + IT(SBクリエイティブ)の 『第4次産業革命のビジネス実務論』、Arm Treasure Data PLAZMAの 『福本 勲の「プラットフォーム・エコシステム」見聞録』がある。その他 Web コラムなどの執筆や講演など多数。
鍋野 敬一郎
フロンティアワン 代表取締役 1989年3月 同志社大学工学部化学工学科卒業(生化学研究室)。 1989年米国総合化学デュポン(現ダウ・デュポン)入社、1998年独ソフトウェアSAPを経て、2005年にフロンティアワン設立。業務系(プロセス系:化学プラントや医薬品開発など、ディスクリート系:組立加工工場や保全など)の業界および業務、システムの調査・企画・開発・導入の支援に携わる。2015年より一般社団法人 インダストリアル・バリューチェーン・ イニシアティブ(IVI) サポート会員となり、総合企画委員会委員、エバンジェリストなどをつとめる。また、オンラインメディア IoTNEWSを運営するアールジーンのアドバイザー、エッジAIベンチャーのエイシングのアドバイザーなどをつとめる。その他Web コラムなどの執筆や講演など多数。
幸坂 知樹
電通国際情報サービス X(クロス) イノベーション本部 本部長補佐。1988年3月横浜市立大学文理学部卒業(国際関係課程)。 1988年電通国際情報サービスに入社、CRM、ERP、インターネット関連SI、デジタル・マーケティング、IoT、ビッグデータ、AIのソリュー ション事業の立ち上げに携わる。2015年より一般社団法人インダストリアル・バリューチェーン・イニシ アティブ(IVI) サポート会員となり、教育普及委員会委員などをつとめる。その他講演など多数。
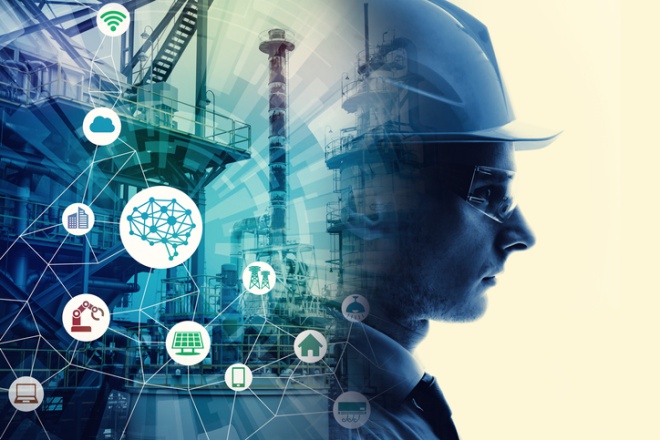
1つの国、企業だけで完結するモノづくりの限界
プラットフォーム・エコシステムのビジネスモデルを説明する前に、ここに至る日本のモノづくりの経緯について、サプライチェーンの視点から整理する。第2次世界大戦(太平洋戦争)の敗戦後、日本のモノづくりは世界最大の市場を持つ米国のサプライチェーンの一部を担うことで、急速な回復発展を遂げた。昭和初期の日本の製造業を支えていたのは、職人技に支えられたモノづくり技術であった。日本の近代化は、鉄鋼などの重工業や繊維産業を支える機械化からはじまった。大量生産の技術は、機械設備の大規模投資が可能な官営工場や軍需産業などを背景とした財閥や大企業のみが保有していた。町工場の大半は、小規模であり、モノづくりの全工程を職人が手掛ける手工業的な生産であった。
敗戦後、日本の製造業は、米国の大量生産技術に学ぶことで一気に発展成長することになる。軍需産業で培った航空機や船舶のブロック工法などの生産技術は自動車や産業機械分野で生かされ、大量生産における短納期と品質管理を大きく進化させた。繊維産業で培った緻密で高度な縫製技術は、家電やハイテクなどの小型化・高機能化へ引き継がれた。戦後復興期から1970年代以降の高度成長期へと、日本の製造業は発展してきたのである。
日本の産業構造の特徴は、完成品を生産する大企業と、その部品を生産する中小企業がピラミッド型生産組織を生み出したことにある。大企業がトップに立つことで、中小企業が苦手とする安定した需要の確保と、生産に必要な原材料や設備の手配を可能とした。国内市場では、自動車や産業機械などで複数の企業グループが競争を展開することとなった。
世界最大の市場を持つ米国では日本製品の位置づけは低く、日本製品が米国市場で競合として認知されたのは1970年代になってからであり、それ以降高まりを見せた。米国の製造業は、1990年代のリセッションで大きく衰退し、米国は製造業の代わりにコンピュータや金融など情報産業を基幹産業とした。このタイミングでコンピュータを利用した第3次産業革命がはじまった。結果的にコンピュータ化による生産性向上の恩恵を受けたのは日本の製造業であった。
日本で実用化された第3次産業革命のノウハウや生産技術は、安い人件費と豊富な労働力を持つ中国やアジア新興国へ広がった。日本企業は、米国市場を最優先としていたが、中国やアジア新興国は欧州市場にも近く、2000年代半ば以降、中国は「世界の工場」と呼ばれる工業化に成功した。
製造大国ドイツの焦りから生み出された「インダストリー4.0」
日本や中国、アジア新興国の影響力が大きくなり、製造業の比率が高い産業構造を持つドイツは大きな危機感を抱いた。2005年当時では、労働者1人当たりの賃金が、ドイツと中国で8倍から10倍もの格差があった。このままでは高賃金のドイツに、勝ち目がないことは明白であった。そこで考え出されたのが「インダストリー4.0」と名づけた新しいモノづくりによる製造業のルール変更であった。ドイツの狙いは、自国の製造業を守るために中国にサプライチェーンの一部を担ってもらうことにあった。米国が日本にサプライチェーンの一部を担ってもらったのと、同様のことを目論んだのである。米国がコンピュータなど情報産業と金融業に基幹産業をシフトしたのに対して、ドイツは基幹産業を製造業から他の産業へ移すのではなく、生産のデータと物流のデータをネットワークでつないでドイツと中国で役割分担をすることで、生き残ることを目指した。
【次ページ】産業用IoTプラットフォームが目指すべきはiPhoneやiOS
製造業界のおすすめコンテンツ
製造業界の関連コンテンツ
PR
PR
PR