- 会員限定
- 2017/02/13 掲載
「SEMIスタンダード」からIoTが学ぶこと いかに標準化を進めるか?
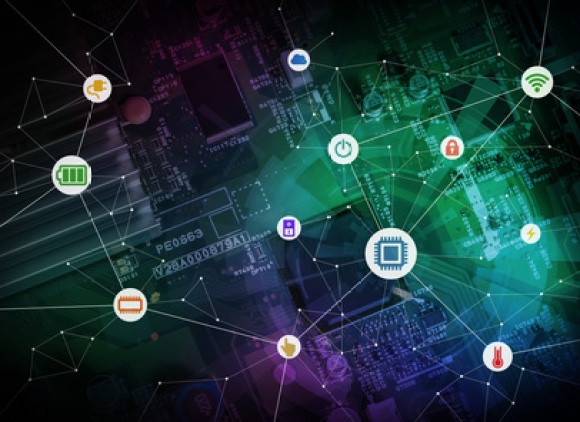
古くから標準化が進んだ半導体から、IoTは何を学べるのか
あらゆる産業を巻き込んで進展するIoTには、その「標準化」が強く求められている。2016年12月に開催された「SEMICON JAPAN」で、横河ソリューションサービスのソリューションビジネス本部 ビジネスマネジメント部 部長 藤沢 尚人氏が登壇。ひと足早くデジタル化・ネットワーク化が進んだ半導体製造において、広く利用されている業界自主基準「SEMIスタンダード」(SEMI規格)が果たした役割と利点を整理することで、IoTの標準化の道筋を紐解いた。横河ソリューションサービスは、計測・制御機器分野で世界的なシェアを持つ横河電機の国内販売・エンジニアリング部門と、保守サービスを実行する横河フィールドエンジニアリングサービス、情報エンジニアリングを担ってきた横河ソリューションズを統合し、2013年4月に誕生した会社だ。なぜ、同社の藤沢氏が「IIoT階層モデルにおけるSEMIスタンダードの位置づけと利点」といったテーマで語るのか。
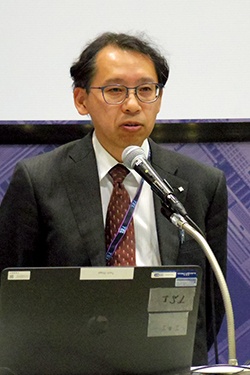
ソリューションビジネス本部
ビジネスマネジメント部 部長
藤沢 尚人氏
IoT活用には、新しく得られたデータを使うビジネスが生まれるという面もあるが、製造業視点でIoT活用を見ると、自分が作っているものがネットワークにつながること自体で付加価値が付く、という面もある。「特に半導体製造における製造ラインの付加価値向上という点で、SEMIスタンダードが果たしてきた役割について解説してきたい」と藤沢氏は語った。
なぜ半導体製造にSEMIスタンダードが導入されたのか
半導体製造においては、かなり昔から製造装置の動きを管理するシステムを構築してきた。藤沢氏は「半導体製造におけるSEMIスタンダードがなぜ作られてきたかというと、早くデータをデジタル化しないと扱えなかったからだ」と語る。
何百もの工程を繰り返して半導体は製造されるため、今どこの作業をしているのかが分かりづらい。製造されているモノを見ても分からないので、その状況を知るためにはデータ化する必要があった。しかしそのデータ量は非常に膨大になるので、1か所にまとめて管理することはできない。
ほかにも製造現場ではクリーンルームを導入せざるを得ないが、クリーンルームはコストがかかるので24時間365日動かしたい。また半導体製造装置自体が高価で、早く設備投資を回収したいという考えも起きる。そんな高い装置を使っているのにもかかわらず、微細化、集積密度により製造プロセスはどんどん変わっていく。すると製造工場の装置も入れ変わってくる。製造装置が入れ替わってもラインがつながるようにするために、スタンダード化が必要となった。このためデータをデジタル化し、ネットワークにあげて管理するという方式が早くから採られたわけだ。
【次ページ】 スタンダードが決まることで生まれた効果
製造業界のおすすめコンテンツ
製造業界の関連コンテンツ
PR
PR
PR